Hark
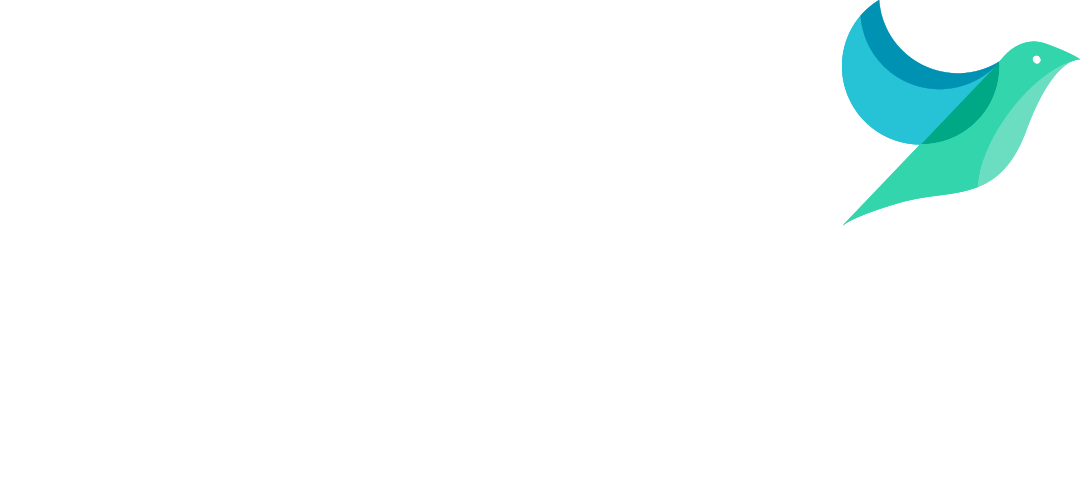
Asda's IPL partners with Hark on Energy Monitoring and Asset Performance Project
IPL (International Procurement & Logistics) had a vision to improve efficiency in their facilities and are achieving this using Hark’s industrial IoT and energy analytics software. The two areas of focus for the project were energy monitoring and asset performance.
IPL (International Procurement & Logistics), a part of the ASDA family, source a variety of different products from around the world, specifically for Asda customers, ranging from fresh fruit and vegetables to house plants and flowers; and award-winning wines.
Hark, recently acquired by NASDAQ listed company, SolarEdge, is an award-winning Energy Management and Industrial IoT company based in Leeds, UK.
Founded in 2016, Hark’s technology enables enterprises to improve efficiency, reduce waste and maximise yield by connecting to, providing visibility of, and automatically controlling assets such as energy meters, building management systems, energy storage systems and industrial systems, regardless of manufacturer.
Hark are now working with IPL, one of the largest importers of produce in the UK, to gain connectivity and visibility of industrial assets within multiple packaging sites in the UK. The initial goal was to retrieve energy and asset performance data to feed into the company’s OEE (overall equipment effectiveness) metrics.
IPL’s facilities contain production lines, refrigeration plants, and multiple sub-metered areas throughout. Working with Hark’s IoT software, IPL has a central location to visualise and analyse their energy and process data.
In order to make substantial performance gains and energy savings, IPL were aware that they would need cloud connectivity to a real-time asset and energy management system.
Hark connected IPL’s industrial assets and meters to the cloud, to feed process, power and energy data directly into the Hark Platform using the existing secure network in the facility.
The Hark Platform gives users the ability to see real-time energy data, plant performance data and real-time process line data that is set up in custom dashboards. This data allows users to start identifying where potential energy savings can be made and highlight inefficiencies across the site.
Commenting on the partnership, Patrick Waterton, Manager of Engineering & Hygiene at IPL said:
“Having a deeper understanding of what’s happening behind the scenes at our production sites has been a real game-changer for how IPL makes operational and capital decisions. The Hark Platform gives me and my team the insight we need to keep our assets running at peak efficiency and to identify potential improvement initiatives, which ultimately helps to reduce operational and energy costs.” – Patrick Waterton - Manager of Engineering & Hygiene, IPL
We are looking for businesses to interview.
CONTACT USPlease contact us and increase your company online visibility